Indice
- Introducción
- Principios generales de la resistencia cerámica
- Resistencia mecánica: ensayos normativos y factores influyentes
- Resistencia al desgaste y a la abrasión: clasificación PEI
- Resistencia térmica y choque térmico: comportamiento en ciclos térmicos
- Resistencia química: ensayos y condiciones de exposición
- El papel de los materiales vitrificantes en la resistencia
- Control de calidad y optimización de los parámetros
- Innovaciones tecnológicas para mejorar la resistencia
- Aplicaciones industriales y elección de materiales
- Conclusión
- Preguntas frecuentes
Introducción
Cuando se habla de resistencia cerámica, se hace referencia a la capacidad de un material para mantener sus características estructurales y funcionales en presencia de solicitaciones de diversa índole. Comprender cómo funciona la resistencia cerámica es fundamental para quienes trabajan en el diseño y la producción de superficies de alto rendimiento, como baldosas, revestimientos y superficies técnicas.
Los principales tipos de resistencia relevantes en el ámbito industrial incluyen:
- Resistencia mecánica, es decir, la capacidad de soportar flexión, compresión e impacto sin fracturarse. Fundamental para suelos y superficies sometidas a cargas.
- Resistencia a la abrasión y al desgaste, especialmente importante en entornos comerciales e industriales con mucho tránsito, donde se requiere durabilidad en el tiempo.
- Resistencia térmica y al choque térmico, esencial para superficies expuestas a ciclos de calor y frío o a altas temperaturas, como en exteriores o en entornos productivos.
- Resistencia química, necesaria en entornos expuestos al contacto con ácidos, bases, detergentes y disolventes, como en el sector alimentario, sanitario o químico.
Estos aspectos determinan la funcionalidad y durabilidad del material cerámico y guían la elección de los productos más adecuados en función de las condiciones de uso.
Principios generales de la resistencia cerámica
La resistencia de un material cerámico viene determinada en gran medida por su estructura interna y por las interacciones químico-físicas entre los componentes que lo constituyen. Las siguientes características son fundamentales para comprender su comportamiento en aplicaciones industriales:
Estructura cristalina y enlaces atómicos
Los materiales cerámicos están constituidos por una combinación de fases cristalinas y vítreas. Las fases cristalinas presentan estructuras reticulares regulares, en las que los átomos están unidos mediante enlaces iónicos o covalentes, ambos caracterizados por una elevada energía de enlace. Esta configuración confiere rigidez y estabilidad, pero limita la deformabilidad plástica, haciendo que la cerámica sea más susceptible a la fractura si se somete a esfuerzos elevados y concentrados.
Mecanismos fundamentales de resistencia
A nivel molecular, la resistencia depende de la continuidad de la red cristalina y de la ausencia de defectos estructurales que puedan actuar como puntos de inicio de las fracturas. Los mecanismos de cohesión entre los granos, la adherencia entre las fases y la distribución homogénea de las partículas contribuyen de manera determinante al rendimiento mecánico y térmico.
Influencia de la porosidad y la microestructura
La porosidad residual, si es excesiva o está mal distribuida, reduce la resistencia del material. En los procesos cerámicos industriales, se tiende a minimizar la presencia de poros abiertos o cerrados mediante el ajuste de los parámetros de cocción, la granulometría y el prensado. La microestructura resultante de un proceso optimizado presenta granos uniformes y fases bien integradas, lo que favorece la resistencia mecánica y la resistencia a la abrasión.
Teoría de la propagación de microfracturas
Las cerámicas, al ser materiales frágiles, están sujetas a roturas de tipo frágil, es decir, sin deformación plástica previa. Las microfracturas se desencadenan en presencia de defectos estructurales y se propagan rápidamente bajo cargas críticas. Las pruebas normativas (por ejemplo, ISO 10545-4) evalúan la resistencia a la flexión precisamente en función de esta vulnerabilidad. La calidad de la sinterización y la homogeneidad de la masa cerámica son elementos fundamentales para contener la propagación de las fracturas.
Resistencia mecánica: flexión, compresión, impacto.
La resistencia mecánica es un parámetro fundamental para evaluar la idoneidad de los materiales cerámicos en aplicaciones sometidas a cargas estáticas y dinámicas. Las normas internacionales, como la ISO 10545-4, definen los métodos para medir la resistencia a la flexión y a la compresión en laboratorio.
Análisis de la resistencia a la flexión
La resistencia a la flexión (también denominada módulo de rotura) mide la capacidad del material para resistir una fuerza distribuida sobre una superficie. Se evalúa aplicando una carga sobre una baldosa apoyada en dos puntos, hasta el punto de rotura. Los valores resultantes varían en función de:
- dimensión y espesor de la muestra
- regularidad y densificación de la microestructura
- presencia de microfisuras internas
Una mayor uniformidad del cuerpo cerámico y una cocción bien controlada contribuyen a aumentar la resistencia a la flexión.
Resistencia a la compresión: mecanismos y valores
Los materiales cerámicos toleran muy bien las cargas compresivas gracias a la naturaleza rígida de su red cristalina. La resistencia a la compresión se mide mediante cargas verticales crecientes sobre probetas de dimensiones controladas. También en este caso, el valor depende de la densidad del material y de la ausencia de porosidad o inclusiones. La prueba es menos habitual que la de flexión, pero es importante en ámbitos estructurales o para aplicaciones verticales (por ejemplo, revestimientos portantes).
Resistencia al impacto y tenacidad de los materiales cerámicos
La resistencia al impacto es menor en los materiales cerámicos que en otros materiales estructurales, debido a su baja tenacidad. La tenacidad describe la capacidad de absorber energía sin fracturarse. Para verificarla, se utilizan ensayos como la caída de masa sobre probetas cerámicas o instrumentos específicos para medir la propagación de fracturas. Por lo general, una cerámica con una estructura homogénea y espesores uniformes presenta una mayor resistencia a pequeños impactos localizados.
Pruebas normativas de referencia
Las principales pruebas normativas para evaluar las propiedades mecánicas incluyen:
- ISO 10545-4: Determinación de la resistencia a la flexión y a la rotura
- ASTM C1161: Método para la flexión en probetas rectangulares de cerámica (aplicado principalmente a la cerámica técnica)
Estas pruebas están estandarizadas para garantizar la comparabilidad de los resultados entre diferentes materiales, fabricantes y condiciones de ensayo. La documentación de las pruebas suele ser necesaria en las fichas técnicas de los productos destinados a entornos con altas exigencias.
Resistencia al desgaste y a la abrasión
La resistencia al desgaste es una de las propiedades más importantes de los materiales cerámicos destinados a su uso en pavimentos y superficies con mucho tránsito. El desgaste puede estar causado por la fricción mecánica, el roce, la presencia de residuos abrasivos o la movimentación de cargas. El comportamiento del material en estos contextos es determinante para su durabilidad en el tiempo.
Mecanismos de desgaste superficial en materiales cerámicos
En los materiales cerámicos, el desgaste se produce por la eliminación progresiva del esmalte o de la superficie externa del soporte. La acción mecánica constante de zapatos, ruedas, arena y otros agentes abrasivos puede generar micro-surcos, pérdida de brillo o, en los casos más graves, eliminación de material y alteración cromática.
El usura se distingue en:
- abrasión superficial (brillo, acabado)
- abrasión profunda (estructura, color, esmalte)
Factores que influyen en la resistencia a la abrasión
Diversos factores contribuyen a determinar el grado de resistencia al desgaste de un material cerámico:
- Tipo de esmalte o acabado: Los esmaltes vitrificados de alta dureza garantizan una mayor resistencia.
- Densidad y porosidad del soporte: Un soporte poroso tiende a ceder más rápidamente bajo el estrés abrasivo.
- Espesor de la capa superficial: Cuanto mayor sea el espesor útil, mayor será la resistencia del material a la erosión.
- Granulometría de los agentes abrasivos: las arenas finas pueden ser más insidiosas que las gruesas.
Clasificación PEI y métodos de ensayo para el desgaste
El método normativo de referencia para determinar la resistencia al desgaste es la norma ISO 10545-7, que define la clasificación PEI (Porcelain Enamel Institute). Esta metodología prevé la exposición de la muestra cerámica a ciclos de abrasión estandarizados con agentes abrasivos específicos.
La escala PEI se articula de la siguiente manera:
Clase PEI | Uso recomendado |
PEI 1 | Baños y dormitorios (tráfico ligero) |
PEI 2 | Zonas residenciales excluidas cocinas y entradas. |
PEI 3 | Zonas residenciales de uso moderado |
PEI 4 | Ambientes residenciales y comerciales con tráfico medio. |
PEI 5 | Ambientes públicos, industriales y comerciales intensos. |
La prueba mide la variación del aspecto superficial y la pérdida de material en función de los ciclos.
El papel de los esmaltes y los tratamientos superficiales en la resistencia al desgaste
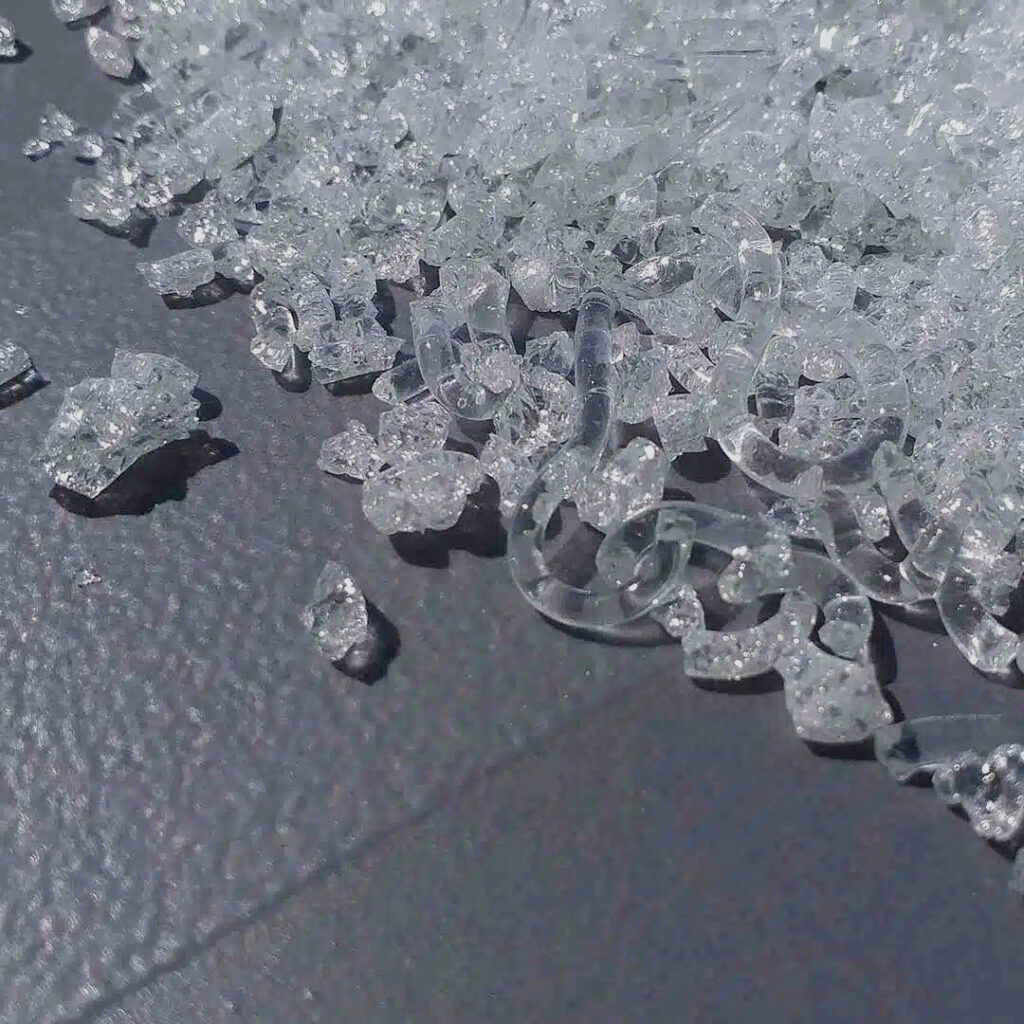
La elección del esmalte y de los materiales vitrificantes influye directamente en la resistencia a la abrasión de las superficies cerámicas. Los esmaltes con composición vitrificada y alta dureza contribuyen a mejorar la resistencia superficial. En función de las necesidades de aplicación, se pueden adoptar diferentes tecnologías superficiales basadas en granos técnicos.
Sicer ofrece una amplia gama de granallas de alta resistencia diseñadas para aumentar el rendimiento superficial. Entre ellas:
- La línea NEXT EXPERIENCE SURFACES, realizada con microgranulos de granulometría calibrada, permite obtener superficies opacas, antirreflectantes, resistentes a los agentes químicos y fáciles de limpiar.
- la serie GHR – High Resistance Grits, diseñada para suelos sometidos a intensas tensiones, permite obtener superficies naturalmente texturizadas, antideslizantes, resistentes a la abrasión y con un excelente rendimiento gráfico incluso en tonos oscuros;
- la línea GRA – Dry Lux, específica para aplicación en seco y pulido espejo, permite obtener superficies extremadamente brillantes y compactas, con alta resistencia química, facilidad de limpieza y planitud, gracias a una selección optimizada de frita y granulometría calibrada.
Todas estas soluciones integran la experiencia de Sicer en el diseño de materiales superficiales que conciliarán la estética y el rendimiento técnico, adaptándose a diferentes ciclos de producción y destinos de uso.
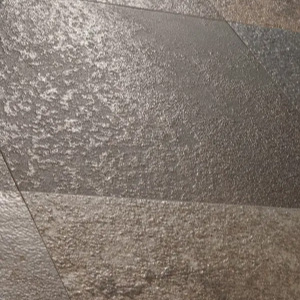
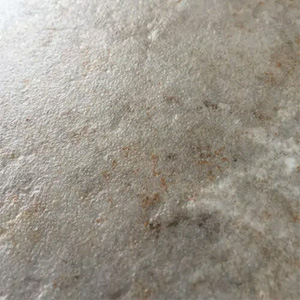
Resistencia térmica y choque térmico
Los materiales cerámicos, por su naturaleza inorgánica y no metálica, poseen una buena estabilidad térmica, lo que los hace adecuados para aplicaciones en entornos sujetos a variaciones de temperatura incluso significativas. Sin embargo, el comportamiento ante las solicitaciones térmicas depende de diversos factores microestructurales y debe evaluarse mediante ensayos específicos.
Comportamiento de los materiales cerámicos ante las variaciones de temperatura
Las cerámicas responden a las variaciones térmicas con expansiones y contracciones volumétricas, que pueden generar tensiones internas, sobre todo en presencia de fases heterogéneas o discontinuidades estructurales. Si las solicitaciones superan el umbral de elasticidad del material, pueden producirse microfracturas o delaminaciones entre el esmalte y el soporte.
Coeficiente de dilatación térmica y sus implicaciones
El coeficiente de dilatación térmica lineal (α) mide la variación dimensional del material en función de la temperatura. Una compatibilidad insuficiente entre el coeficiente del soporte y el del esmalte puede generar tensiones diferenciales durante la cocción o en las fases de uso, comprometiendo la resistencia mecánica y la integridad estética del producto.
La optimización de las composiciones cerámicas requiere, por lo tanto, una selección equilibrada de materias primas y vitrificantes para reducir las diferencias entre las fases implicadas.
Resistencia al hielo y a los ciclos térmicos
La resistencia al hielo es un requisito fundamental para los materiales cerámicos destinados al exterior. Las pruebas previstas por las normas UNI e ISO (como la ISO 10545-12) contemplan ciclos de congelación y descongelación en presencia de agua para simular las condiciones reales de exposición. La posible porosidad residual, si es abierta y capilar, puede absorber agua y provocar roturas internas como consecuencia de la expansión por congelación.
La calidad del prensado y la ausencia de microcavidades son esenciales para garantizar una buena resistencia al hielo.
Choque térmico: causas, mecanismos y prevención
El choque térmico está causado por variaciones rápidas y significativas de temperatura (por ejemplo, pasando de +150 °C a temperatura ambiente), que pueden generar roturas repentinas en materiales con baja conductividad térmica o alta rigidez.
La norma ISO 10545-9 define los criterios de ensayo para el choque térmico en baldosas esmaltadas, sometiendo las muestras a inmersiones alternas en agua fría y caliente. Un producto se considera conforme si, al final del ciclo, no presenta signos evidentes de deterioro (grietas, desprendimientos, variaciones de brillo o color).
El diseño óptimo del ciclo de cocción, el uso de materias primas con elevada estabilidad térmica y la ausencia de porosidad residual son factores clave para prevenir los daños causados por el choque térmico.
Resistencia química y a agentes agresivos
La resistencia química es una propiedad fundamental para los materiales cerámicos destinados a entornos industriales, sanitarios, laboratorios, cocinas profesionales o zonas exteriores expuestas a agentes contaminantes. Indica la capacidad de la superficie cerámica para mantener inalteradas sus características cuando entra en contacto con agentes químicos potencialmente corrosivos o alterantes.
Mecanismos de ataque químico sobre materiales cerámicos
La agresión química puede producirse por solubilización selectiva de los componentes vítreos, alteración del color, opacificación, formación de manchas o modificaciones superficiales. Los materiales más susceptibles son aquellos con una fase vítrea inestable o con porosidad residual accesible, lo que facilita la penetración de líquidos reactivos.
La acción puede ser:
- superficial, con pérdida de brillo o variaciones cromáticas
- estructural, en los casos más graves, con debilitamiento de la superficie esmaltada
Resistencia a ácidos, bases y disolventes orgánicos.
Las superficies cerámicas esmaltadas correctamente vitrificadas suelen presentar una buena resistencia a:
- ácidos orgánicos (por ejemplo, ácido cítrico, láctico)
- ácidos inorgánicos diluidos (por ejemplo, ácido clorhídrico, sulfúrico)
- bases alcalinas (por ejemplo, sosa cáustica, amoniaco)
- disolventes orgánicos (por ejemplo, alcohol, detergentes profesionales)
Sin embargo, el rendimiento depende de la composición del esmalte, el nivel de cocción y el acabado. Una superficie porosa o no completamente sinterizada puede estar más expuesta al ataque químico.
Comportamiento en presencia de sales y agentes atmosféricos
La exposición a sales de deshielo (como el cloruro de sodio o el calcio), lluvias ácidas, humedad y agentes atmosféricos puede alterar con el tiempo el aspecto y la funcionalidad de las superficies que no están adecuadamente protegidas. Por lo tanto, en ambientes exteriores es fundamental utilizar productos impermeables, con vitrificación completa y mínima absorción de agua.
Las condiciones de instalación (juntas, sellados, pendiente) también influyen en la capacidad del material para resistir durante mucho tiempo en condiciones ambientales adversas.
Pruebas de resistencia química según normas internacionales.
Las prestaciones de los materiales cerámicos frente a los agentes químicos están reguladas por normas internacionales:
- ISO 10545-13: verifica la resistencia de las baldosas esmaltadas al ataque químico de ácidos y bases, clasificadas según el tipo de alteración visible o detectable
- ISO 10545-14: evalúa la resistencia a las manchas, importante sobre todo para superficies utilizadas en entornos sanitarios, domésticos o comerciales
Las muestras se someten a una exposición prolongada a sustancias agresivas y el resultado se clasifica en función del efecto producido (sin cambios, opacidad, variación de color, etc.).
El papel de los materiales vitrificantes en la resistencia
Los esmaltes cerámicos y los materiales vitrificables desempeñan un papel fundamental en la determinación del rendimiento superficial del producto acabado, ya que influyen directamente en sus propiedades mecánicas, químicas y de resistencia al desgaste.
Cómo influyen los esmaltes y los materiales vitrificables en las propiedades de resistencia
El esmalte es la capa exterior del material cerámico y puede formularse para ofrecer:
- Mayor resistencia a la abrasión (gracias a la presencia de fases vítreas duras y estables)
- Protección contra agentes químicos y manchas
- Resistencia al choque térmico y a los cambios ambientales
Además, la aplicación uniforme del esmalte y la buena compatibilidad de la expansión térmica con el sustrato evitan el desprendimiento o la aparición de microfisuras con el paso del tiempo.
Formulaciones específicas para aumentar la resistencia superficial.
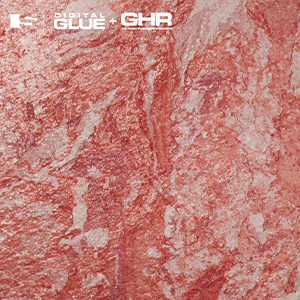
Los materiales vitrificables de alto rendimiento se desarrollan mediante combinaciones cuidadosamente calibradas de fritas, granos, pigmentos y aditivos, con el objetivo de mejorar:
- la compacidad de la capa superficial
- la resistencia a los arañazos y al desgaste
- la resistencia a la corrosión química
Tecnologías innovadoras para un mejor rendimiento
La evolución de las tecnologías cerámicas ha llevado al desarrollo de materiales vitrificables:
- Listo para usar, para una aplicación rápida y controlada
- Con aditivos funcionales integrados para aumentar la resistencia y la adhesión
- Adecuado para ciclos de cocción optimizados para la estabilidad de la superficie
Estas soluciones están diseñadas para reducir los defectos estéticos y garantizar un alto rendimiento incluso en entornos exigentes.
Equilibrio entre estética y propiedades técnicas en los esmaltes
Uno de los principales retos en el diseño de esmaltes cerámicos es lograr un equilibrio eficaz entre el rendimiento técnico (resistencia al desgaste, facilidad de limpieza, compatibilidad térmica) y la calidad estética (brillo, profundidad, uniformidad). Los esmaltes de alta dureza deben seguir cumpliendo los siguientes requisitos:
- mantener el brillo o el acabado mate deseados
- garantizar una excelente reproducción del color, incluso en gráficos complejos
- asegurar la uniformidad y estabilidad de la superficie en formatos grandes
Sicer afronta este reto con una investigación continua en materias primas, pigmentos, fritas y aditivos, desarrollados para integrarse perfectamente en los ciclos de producción más avanzados.
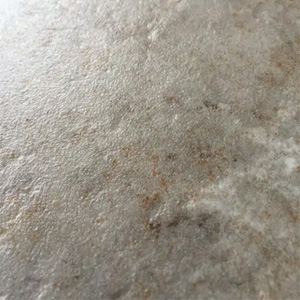
Un ejemplo concreto es la serie GRA – Dry Lux, diseñada para la aplicación en seco con posterior pulido espejo. Estos granos transparentes y compactos permiten obtener superficies muy brillantes con una transparencia total similar al vidrio, resistencia a los arañazos, excelente facilidad de limpieza y un coeficiente de expansión térmica controlado. Su estructura mínimamente porosa y su respuesta óptica optimizada realzan los colores digitales, garantizando excelentes resultados estéticos en todos los formatos. Sicer confirma así su posición como socio tecnológico para las empresas cerámicas que buscan materiales de recubrimiento de alto rendimiento que satisfagan requisitos funcionales y expectativas estéticas cada vez más sofisticados.
Control de calidad y optimización de la resistencia
El mantenimiento del rendimiento de los materiales cerámicos depende en gran medida del control de las fases del proceso. Un sistema eficaz de control de calidad permite verificar la constancia de las propiedades mecánicas, químicas y superficiales, y corregir cualquier desviación que pudiera comprometer la resistencia final del producto.
Metodologías para el control de las propiedades de resistencia en la producción
Las empresas cerámicas adoptan protocolos de muestreo y pruebas periódicas en lotes de producción, con ensayos realizados de conformidad con las normas internacionales (por ejemplo, ISO 10545). Las propiedades controladas incluyen:
- resistencia a la flexión (ISO 10545-4)
- resistencia a la abrasión (ISO 10545-7)
- choque térmico (ISO 10545-9)
- resistencia química y a las manchas (ISO 10545-13, -14)
Los resultados se comparan con las especificaciones técnicas esperadas y pueden registrarse en sistemas de control estadístico de procesos (SPC) para garantizar la trazabilidad y la eficiencia.
Parámetros del proceso que influyen en la resistencia final
Las principales variables que influyen en el rendimiento mecánico y superficial del material incluyen:
- temperatura y curva de cocción
- tiempo de permanencia en el pico
- grado de prensado y compactación de la masa
- humedad residual en las piezas crudas
- distribución de la granulometría
Incluso pequeñas variaciones en estos parámetros pueden modificar la porosidad residual, la sinterización y la cohesión interna de la estructura cerámica, influyendo negativamente en la resistencia.
Técnicas de optimización de los ciclos de cocción para maximizar la resistencia.
El ciclo de cocción es uno de los elementos más críticos para obtener superficies cerámicas de alto rendimiento. Las técnicas de optimización incluyen:
- Regulación precisa de la curva de calentamiento y enfriamiento
- Mantenimiento estable de la temperatura máxima
- Adaptación del ciclo al tipo de esmalte o material vitrificante utilizado
El objetivo es conseguir una vitrificación homogénea, evitando tensiones internas, burbujas, defectos superficiales o irregularidades que puedan debilitar el producto.
Correlación entre la composición química y las propiedades finales
La composición química de la pasta y del esmalte influye directamente en la resistencia del material. La elección y la dosificación de:
- fundentes (boratos, alcalinos)
- materiales refractarios (sílice, alúmina)
- aditivos específicos (opacantes, estabilizantes)
deben estudiarse en función del resultado de rendimiento deseado. El equilibrio entre las fases cristalinas y vítreas, el grado de reactividad entre los componentes y la compatibilidad térmica entre el esmalte y el soporte son elementos determinantes para obtener materiales resistentes, duraderos y conformes con los estándares de calidad del mercado.
Innovaciones tecnológicas para mejorar la resistencia
El sector cerámico está evolucionando rápidamente gracias a la introducción de nuevas tecnologías y formulaciones orientadas a aumentar el rendimiento. Las innovaciones se centran en la mejora de la resistencia mecánica, química y térmica, para responder a las exigencias de los contextos de aplicación más severos.
Aditivos y materiales funcionales para mejorar las propiedades mecánicas
La integración de aditivos funcionales en las formulaciones de esmaltes y soportes representa una estrategia eficaz para mejorar el rendimiento. Entre las soluciones más utilizadas en el sector se encuentran:
- uso de granulados de alta dureza para reforzar la superficie esmaltada
- optimización de la distribución granulométrica para aumentar la densidad y reducir la porosidad
- introducción de opacantes estables para reforzar la cohesión superficial
Estas soluciones contribuyen a aumentar la resistencia al desgaste y la estabilidad en entornos químicamente agresivos o sujetos a frecuentes esfuerzos mecánicos.
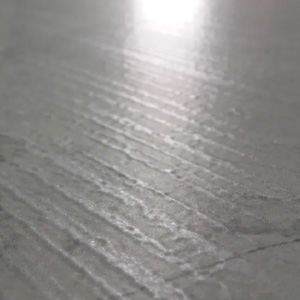
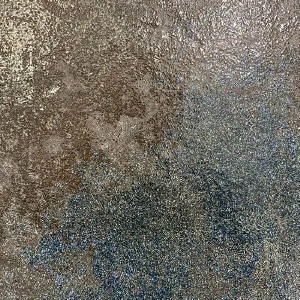
Tecnologías avanzadas de tratamiento superficial
Además de la composición, el rendimiento superficial también se puede mejorar mediante tratamientos físico-químicos aplicados en la fase final del proceso de producción. Entre las prácticas más comunes se encuentran:
- uso de esmaltes autolimpiantes o antibacterianos mediante la integración de componentes específicos
- técnicas de cocción multietapa que optimizan la distribución de las tensiones internas
- mejora de la compatibilidad termomecánica entre el esmalte y el soporte
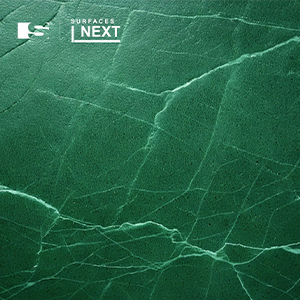
En el caso de los productos NEXT EXPERIENCE SURFACES de Sicer, la innovación reside en la mezcla lista para usar con microgranulos calibrados, que permite una aplicación homogénea, una excelente limpieza y una alta resistencia a los agentes químicos y a la abrasión.
Avances en la formulación de materiales de alta resistencia
La investigación cerámica ha permitido definir formulaciones ad hoc para aplicaciones específicas, actuando sobre los siguientes aspectos:
- selección de fritas con alto contenido en sílice o alúmina
- control de la cristalización de las fases vítreas para mejorar la compacidad
- estudio del comportamiento en el ciclo térmico para garantizar la estabilidad en condiciones reales de uso
Las formulaciones se prueban según las principales normas ISO para verificar su estabilidad mecánica, química y térmica.
Productos innovadores para aplicaciones específicas sometidas a grandes esfuerzos
La innovación también se expresa a través del desarrollo de líneas de productos dedicadas a entornos con altas prestaciones, como:
- pavimentos industriales para tráfico intenso
- revestimientos para exteriores expuestos al hielo, los rayos UV y los contaminantes
- superficies técnicas para el sector sanitario o agroalimentario
Estas aplicaciones requieren materiales que garanticen una resistencia prolongada y un mantenimiento mínimo, combinados con características estéticas personalizables.
Aplicaciones industriales y elección de materiales
La elección de los materiales cerámicos para la industria no puede prescindir de una evaluación minuciosa de las prestaciones requeridas en relación con el contexto de aplicación. Las diferentes formas de resistencia (mecánica, química, al desgaste, térmica) deben tenerse en cuenta en la fase de diseño técnico y en las especificaciones del pliego de condiciones.
Criterios de selección basados en requisitos específicos de resistencia
Cada ambiente impone condiciones diferentes, por lo que es necesario identificar:
- el tipo de solicitaciones previstas (tráfico, cargas, golpes, agentes químicos)
- el nivel de frecuencia e intensidad de la exposición
- las normativas de referencia aplicables (por ejemplo, ISO 10545, EN 16165)
A partir de estos datos, se puede seleccionar el sistema cerámico adecuado (formulación + tratamiento + colocación) capaz de garantizar la resistencia mínima certificable y la durabilidad en el tiempo.
Aplicaciones según los diferentes tipos de resistencia requeridos.
Contexto de aplicación | Resistencia prioritaria | Ejemplo de material adecuado |
Entornos industriales y logística | Abrasión, compresión | Gres técnico con acabado estructurado |
Sector alimentario y sanitario | Agentes químicos, manchas | Superficies esmaltadas vitrificadas |
Exteriores en climas fríos/húmedos | Heladas, choque térmico | Gres porcelánico de baja absorción |
Sectores con alta afluencia (comercial) | Desgaste, impacto, facilidad de limpieza | Superficies con clasificación PEI 4-5 |
La relación entre el tipo de entorno y la resistencia requerida es un paso fundamental para evitar daños prematuros o costes imprevistos de mantenimiento y sustitución.
Correlación entre costes, prestaciones y niveles de resistencia
El diseño de superficies de alto rendimiento implica una inversión inicial mayor, pero garantiza un ciclo de vida más largo y una reducción de los costes indirectos. Las empresas del sector de la construcción y la industria están adoptando progresivamente soluciones que maximizan:
- Durabilidad técnica certificada
- Resistencia al desgaste programada
- Facilidad de limpieza y desinfección
Esta visión es coherente con un enfoque basado en el coste del ciclo de vida (LCC) y orientado a la sostenibilidad económica de la inversión.
Tendencias futuras en el desarrollo de materiales de alta resistencia
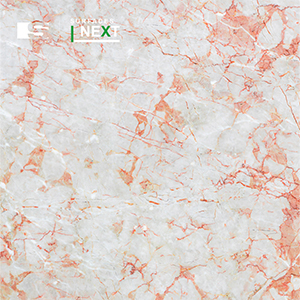
Entre las principales tendencias evolutivas en el sector cerámico se encuentran:
- ampliación de la oferta de formulaciones listas para usar de alto rendimiento
- introducción de superficies con funcionalidades integradas (por ejemplo, antideslizantes, autolimpiantes, antibacterianas)
- optimización de los procesos para reducir el consumo energético y aumentar la eficiencia térmica
- atención creciente a la sostenibilidad de las materias primas y a los ciclos productivos con bajo impacto medioambiental
Sicer, gracias a la constante actualización de sus soluciones y al trabajo de su departamento de I+D, responde a estos retos proponiendo materiales avanzados como NEXT EXPERIENCE SURFACES, capaces de combinar altas prestaciones técnicas con resultados estéticos contemporáneos y aplicabilidad industrial.
Conclusión
Comprender cómo funciona la resistencia cerámica significa saber analizar cada aspecto del material: desde su composición hasta su microestructura y los tratamientos superficiales. Las pruebas normativas son una herramienta fundamental para garantizar que los productos sean adecuados para las condiciones de uso previstas. Soluciones como NEXT EXPERIENCE SURFACES demuestran que es posible integrar un alto rendimiento con la facilidad de uso y características técnicas avanzadas.
FAQ
Depende del tipo de material y de la prueba aplicada. Se mide según normas específicas (por ejemplo, ISO 10545-4 para la flexión).
Estabilidad estructural, durabilidad, resistencia al desgaste, a los agentes químicos y a las variaciones térmicas. Las baldosas cerámicas son ideales para aplicaciones industriales y comerciales.
Esta pregunta se refiere a componentes electrónicos, que no se tratan en este artículo. Aquí se habla de la resistencia estructural de la cerámica en la construcción y la industria.
Las NEXT EXPERIENCE SURFACES son microgranulados opacos y antirreflectantes, ideales para superficies técnicas fáciles de limpiar. Los granulados GHR están diseñados para entornos sometidos a un alto estrés: ofrecen una alta resistencia a la abrasión y un excelente rendimiento gráfico. La serie GRA es específica para aplicaciones en seco y pulido espejo, ideal para obtener superficies extremadamente brillantes y compactas.
Sí. Todos los granules de la gama GHR y GRA se someten a pruebas para garantizar su resistencia a los ácidos (HCl 3 % y 18 %) y a condiciones químicas agresivas, tal y como se indica en las pruebas técnicas incluidas en las fichas técnicas oficiales.
Sí, las GHR son adecuadas para aplicaciones en exteriores. Su resistencia a la abrasión, su transparencia y la posibilidad de crear superficies antideslizantes las hacen ideales también para pavimentos expuestos al tráfico intenso o a los agentes atmosféricos.
Los granules GRA permiten crear superficies pulidas de alto brillo, con excelente planitud, resistencia a los arañazos y ausencia de microporosidad, mejorando así la eficiencia productiva y la calidad estética final.